Building a concrete aquarium is a great idea for avid fish keepers who want to ensure that their fish will be housed securely in a long-lasting and durable container. Creating a concrete aquarium may seem like a daunting task at first glance, but with a little bit of effort and some guidance, you’ll be able to create the perfect habitat for your underwater friends. In this blog, we will discuss everything you need to know about building a concrete aquarium, from selecting the right materials to the various steps involved in the construction process.
If you’re ready to take on the challenge of building a concrete aquarium to house your beloved creatures, then read on to learn more.
Materials Needed
If you’re thinking about building a concrete aquarium, congratulations – you’re in for a fun and rewarding project! Before you start, be sure you have all the materials you’ll need to get the job done right. For starters, you’ll need to select an aquarium mold that’s the right size and shape for your needs. Next, you’ll need to purchase enough concrete mix to fill the mold, as well as any reinforcing materials such as steel mesh or rebar.
You’ll also need a trowel or smoothing tool to help spread out the concrete evenly, and a source of clean water to help the concrete cure properly. Finally, make sure you have protective gear like goggles, gloves, and a dust mask on hand – working with concrete can get messy! With all your tools and materials in place, you’ll be ready to start building your perfect concrete aquarium.
Concrete mix
When it comes to creating a concrete mix, the materials required may vary depending on the project’s scope and size. One of the primary ingredients in any concrete mix is cement. Cement binds particles of sand and gravel to create a concrete mix that can withstand weight and pressure.
Another essential ingredient is water, which activates the cement and helps it dry and set. Aggregates, such as sand and gravel, are also needed to create a consistent mix. Sand provides a smooth texture, while gravel adds strength and durability to the concrete.
Some mixes may require additional materials such as admixtures, which help regulate the setting time or improve workability. In summary, a basic concrete mix requires cement, water, and aggregates, but additional materials may be needed depending on the project’s specific requirements.
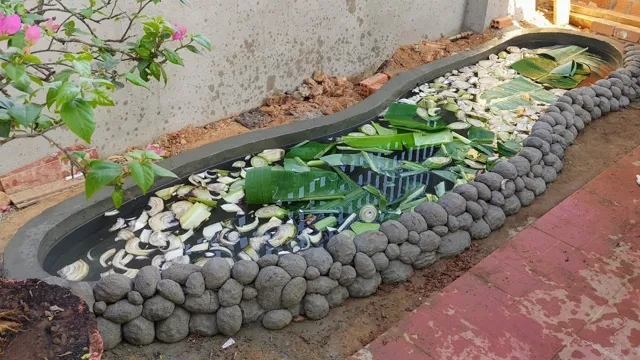
Reinforcement bars
When it comes to construction projects that require reinforced concrete, one of the most important materials needed is reinforcement bars. Reinforcement bars, also known as rebar, are made of strong, durable steel that is designed to provide additional strength to concrete structures by reinforcing them against the tension and compression forces they may encounter. These steel bars are essential to ensuring the structural integrity and stability of buildings, bridges, and other concrete structures.
The size and shape of rebar can vary depending on the specifications of the project, and they are typically produced in long lengths that can be easily cut and bent to fit the necessary dimensions. By incorporating reinforcement bars into a construction project, builders can increase the overall durability and longevity of the structure, ensuring that it will last for years to come even in harsh environmental conditions.
Waterproofing sealant
When it comes to waterproofing your home, using a waterproofing sealant can be an effective solution. However, before applying the sealant, it’s important to have the right materials on hand. First and foremost, you’ll need the waterproofing sealant itself.
There are a variety of sealants available on the market, so make sure to choose one that is suitable for the surface you’ll be applying it on. Next, you’ll need a paintbrush or roller to evenly apply the sealant onto the surface. Making sure you have good lighting is essential to ensure that every inch of the surface is covered.
You’ll also need gloves to protect your hands while applying the sealant and a small bucket to hold the sealant. Finally, make sure to have a clean cloth or rag on hand to clean up any excess sealant and to ensure a smooth finish. Using these materials will help make the process of waterproofing your home as seamless and effective as possible.
Remember to follow all safety precautions when applying the sealant, and don’t hesitate to seek professional help if needed.
Plywood sheets
To start any plywood sheet project, there are a few essential materials needed. First and foremost, you’ll need the plywood sheets themselves. The exact size and thickness will depend on the project you’re working on, so be sure to measure properly before purchasing.
Other essential materials include a saw to cut your plywood to size, sandpaper to smooth out any rough edges, and a drill or screws to attach the plywood to your desired surface. Additionally, depending on the project, you may need wood glue or adhesive to ensure the plywood stays securely in place. While it may seem like a simple project, it’s important to have all the necessary materials before starting to ensure success.
So, gather your materials and get started on your plywood project today!
Wood screws
When it comes to working with wood, choosing the right screws is essential for ensuring a strong and secure hold. Wood screws are specifically designed for use with wood materials and come in a variety of sizes and styles. To determine the right wood screw for your project, consider the type and thickness of the wood you’ll be working with, as well as the overall weight and load-bearing requirements.
Material wise, you’ll need the screws themselves, a drill with appropriate bits for creating pilot holes, and possibly some wood glue for added support. Investing in high-quality wood screws can make a big difference in the overall strength and durability of your woodworking projects, so take the time to choose the right materials for the job.
Release agent
When it comes to creating molds for various objects and products, it’s important to have a release agent on hand. This material is essential for ensuring that the molded object can easily be removed from the mold without damaging the surface or losing its shape. To get started with using a release agent, you’ll need a few key materials.
These include the release agent itself, which can come in various forms such as sprays or liquids, as well as a brush or applicator for spreading the release agent onto the mold surface. You may also want to invest in a mold cleaner to ensure that the surface is properly prepped and ready to receive the release agent. With these materials in hand, you’ll be well-equipped to create clean, precise molds with ease – just be sure to follow the instructions on your chosen release agent carefully for best results. (See Also: How to Glue Rocks Together for Aquarium: A Step-by-Step Guide to Perfectly Secure Rocks in Your Aquarium!)
Preparing the Plywood Form
Building a concrete aquarium requires a sturdy and well-designed form which will serve as the mold in creating a concrete structure. To prepare the plywood form, measure the desired dimensions of your aquarium and cut the plywood accordingly. Make sure to sand the edges of the plywood to ensure a smooth surface.
After cutting, assemble the pieces of the plywood together using screws or nails, creating a waterproof seal between the joints. A tip is to use silicone caulk to seal the plywood to prevent leaks. Before pouring the concrete, cover the interior of the plywood with release oil to prevent concrete from sticking to the mold, making it easier to remove the form once the concrete has set.
Building a plywood form may sound like a simple process, but the key is precision in measurement and the strength of the plywood used. Remember, the form will serve as the foundation of your concrete aquarium, and it needs to be built well to avoid leaks or any structural issues. With a well-built plywood form, you’ll pave the way for a successful aquarium project.
Measure and cut plywood sheets
Preparing the plywood form is an essential step in creating any project that requires a custom shape or size. The first step is to measure and cut the plywood sheets. It sounds easy, but there are some crucial points to keep in mind.
Firstly, you should always use a straight edge or a saw guide to ensure that the plywood is perfectly straight. Any small deviation could result in a poorly fitting form, and that can cause problems down the line. Next, make sure you’re using the right saw blade.
A fine-toothed blade is best for cutting plywood, and it’ll give you a smoother edge. Lastly, be sure to double-check your measurements before cutting. If you’re off by even a fraction of an inch, it can throw off the entire form.
Preparing the plywood form is all about accuracy and attention to detail. By taking these steps seriously, you’ll get a form that’s ready for the next step, whether that’s for concrete pouring or any other use.
Screw plywood together
If you’re looking to create a plywood form for your next woodworking project, one important step is to screw the plywood together properly. This will ensure that the form holds its shape and doesn’t fall apart during use. To do this, you’ll need to gather your materials, including your plywood sheets and the appropriate screws.
Lay your plywood sheets out and make sure they’re even and flush. Then, use your screws to attach them together, making sure to space them out evenly and use enough screws to create a secure bond. This will help your form maintain its shape and last for many uses to come.
So, take the time to properly secure your plywood sheets together before moving on to the next step in your project.
Apply release agent
Before pouring the concrete mix, it’s crucial to prepare the plywood form. One of the most important steps in this process is applying a release agent onto the form. This agent helps to prevent the hardened concrete from sticking to the plywood, which can cause damage to the form and make it difficult to remove the finished product.
There are various types of release agents available, such as petroleum jelly or vegetable oil, but it’s important to choose the one that is appropriate for your project. Applying a release agent is a simple process that involves using a brush or a spray to coat the entire surface of the plywood form evenly. This step ensures that the form is ready, and the final product will come out smoothly and without any damages.
Always remember to apply the release agent before pouring the concrete to ensure the best results.
Mixing and Pouring the Concrete
Mixing and pouring the concrete for your aquarium base is a crucial step when building a concrete aquarium. The process requires precision, attention to detail, and patience. First, ensure that all the necessary tools are available, including a cement mixer, trowel, measuring buckets, water, and cement.
Use a ratio of four parts cement to one part water and mix it in the cement mixer until it is smooth and free of lumps. Then, slowly pour the mixture into the aquarium base, making sure to evenly distribute it and smooth it out with a trowel. It’s essential to avoid creating air pockets or leaving gaps as they can weaken the structure’s integrity.
Once the concrete has been poured, it’s crucial to allow it to cure completely for at least 28 days before adding any water to the aquarium. This curing process ensures that the concrete is strong enough to support the tank’s weight and will not crack or break under pressure. With proper mixing and pouring techniques, your aquarium base will be solid and stable, providing a secure home for your aquatic pets for years to come!
Mix concrete according to instructions
When it comes to mixing and pouring concrete, following instructions is key. To mix the concrete, first gather all the necessary materials such as the cement, sand, and water. Then, follow the instructions on the bag of cement to determine the correct ratio of ingredients.
This will ensure that the concrete sets properly and is strong enough to withstand the weight it will be supporting. Mixing the concrete can be done by hand using a shovel and wheelbarrow or with an electric mixer. Once the mixture is ready, it’s time to pour it into the designated area while making sure it’s spread evenly and levelled. (See Also: How to Get Rid of Green Hair Algae in Aquarium: Effective Strategies)
It’s important to work quickly as the concrete will start to set within 30 minutes. With the right mixture and pouring technique, you can create a strong and durable foundation for your project. So, don’t forget to mix the concrete according to the instructions carefully for best results!
Pour concrete into form
When it comes to pouring concrete into a form, the first step is to ensure that the concrete mix is thoroughly and evenly mixed. The right consistency of the mix is important, as it will greatly impact the final outcome of the project. Mixing the concrete can be done using a mixer or by hand using a wheelbarrow and shovel.
Once the mix is ready, it’s time to pour it into the form, starting at one end and working towards the other. It’s important to work quickly, as the concrete will start to set soon after it’s been poured. While pouring, make sure to tamp down the mix using a tamping tool to eliminate any air pockets.
Remember, the key to a successful pour is to have the right consistency of mix, pour it evenly into the form, and tamp it down to remove any air pockets. Once you’re done pouring the concrete into the form, allow it to cure for at least a day before removing the form. This will ensure that the concrete is properly set and is ready for use.
Insert reinforcement bars
After preparing the foundation, the next step in the process is to insert reinforcement bars. These bars, made of steel, are crucial to the integrity of the structure. They provide added strength, preventing the concrete from cracking or breaking under stress.
Before placing the bars, make sure they are accurately measured and cut to size. Then, lay them out in a strategic pattern, ensuring they are evenly spaced and have the necessary overlap. Once that is done, tie them together using wire mesh or steel ties.
This process may seem tedious, but it is essential to ensure the stability and safety of the structure. Remember, that taking shortcuts at this stage can lead to future problems and costly repairs, so take time to ensure accuracy and thoroughness.
Finishing Touches
To finish off your DIY concrete aquarium, there are a few important touches you should consider. Firstly, it’s crucial to allow your aquarium to cure for at least a few days before filling it with water and fish. This will ensure that the concrete has fully hardened and won’t release any harmful chemicals into the water.
Next, consider sealing the inside of the aquarium with a non-toxic sealant. This will protect both the concrete and the fish from any potential toxins. Finally, add some decorative elements such as rocks and plants to make the aquarium look more natural and provide hiding spots for the fish.
By following these steps, you can enjoy a unique and durable concrete aquarium that will provide a beautiful home for your aquatic pets.
Smooth the surface of the concrete
After pouring concrete, it’s important to smooth the surface to create a polished and professional finish. This process is known as “finishing,” and it involves using special tools to level, smooth, and remove imperfections from the surface of the concrete. One tool commonly used for finishing is a bull float, which is a large, flat tool used to flatten the surface and remove any excess concrete.
Another tool is called an edger, which is used to round the edges of the concrete and give it a smooth and refined look. It’s important to take the time to finish the concrete properly, as this will help to create a durable and long-lasting surface that can withstand heavy use and harsh weather conditions. So, whether you’re working on a small DIY project or a large-scale construction project, taking the time to finish the concrete is a crucial step that should not be overlooked.
Apply waterproofing sealant
After you have installed your tile or masonry project, the final step is to apply a waterproofing sealant. By doing this, you are adding a layer of protection against water damage and ensuring the longevity of your project. Choosing the right sealant is crucial, as there are many options available on the market.
Look for one that is specifically designed for the material of your project and that has a good track record for durability. Once you have selected the sealant, make sure to follow the instructions carefully for application. It’s essential to apply enough of the sealant to create a complete barrier, but not so much that it runs or drips.
Take your time, and remember that the final step of applying the waterproofing sealant will make all the effort and hard work you put into your project worth it in the long run.
Curing and Water Testing
Building a concrete aquarium might seem like a daunting task, but with the right knowledge, it can be a fulfilling experience. One essential step to take before constructing your aquarium is curing the concrete. Curing is the process of letting the concrete harden and gain strength gradually.
This can be done by keeping the concrete moist for a certain amount of time, typically 28 days. Once the concrete is cured, water testing comes into play. It is crucial to test the water before adding any fish or aquatic plant life to the aquarium.
This helps to ensure that the water is a suitable environment for your aquatic creatures to thrive in. It is recommended to test for parameters such as pH level, ammonia, nitrate, and nitrite levels. By taking the time to cure the concrete and test the water, you can have peace of mind in knowing that your concrete aquarium is well-prepared and safe for your aquatic friends.
Let concrete cure for 28 days
When it comes to concrete, curing and water testing are essential steps in the process. Curing refers to the process of allowing the concrete to harden and reach its maximum strength. This is typically done by keeping the concrete moist for 28 days. (See Also: How to Add Magnesium to Aquarium Plants: A Comprehensive Guide for Beginners)
It’s tempting to rush the curing process and move on to the next step, but it’s crucial to be patient and allow the concrete to fully cure before moving forward. Skipping or shortening the curing period can lead to weaker and less durable concrete. Water testing is another important aspect of working with concrete.
This involves testing the water content of the mix to ensure that it’s at the correct ratio for optimal strength. The water-to-cement ratio is critical, as too much or too little water can negatively impact the quality of the concrete. Testing the water content before pouring the concrete can prevent costly mistakes down the line.
In short, curing and water testing are critical steps in the concrete process that can’t be overlooked. By allowing ample time for curing and testing the water content beforehand, you’ll ensure you’re working with the strongest, most durable concrete possible. Don’t rush the process – your patience will pay off in the end.
Fill aquarium with water and check for leaks
When it comes to setting up your aquarium, filling it with water and checking for leaks is an essential step. While it may seem like a straightforward task, there are a few things to consider before pouring in the water. First, make sure your aquarium is placed on a level surface, as any unevenness can cause stress on the glass and lead to leaks.
Once you’ve ensured that the surface is level, fill the aquarium with water slowly, using a hose or pitcher. As you fill the tank, keep an eye out for any leaks or drips, paying close attention to the seams and corners. If you notice any leaks, drain the water and fix them before proceeding.
Once you’re satisfied that the aquarium is leak-free, it’s time to begin the process of cycling and testing the water to ensure that it’s safe for your aquatic pets. By taking the time to properly fill and check your aquarium for leaks, you’ll be well on your way to creating a healthy, thriving aquatic environment for your fish and other underwater creatures.
Conclusion
In conclusion, building a concrete aquarium can be a challenging yet rewarding endeavor. It requires patience, attention to detail, and a willingness to get your hands dirty. But once the tank is complete and filled with aquatic life, it becomes a beautiful display that can be enjoyed for years to come.
Just remember, always use appropriate safety gear and seek professional advice when necessary. So dive in and make a splash with your very own concrete aquarium!”
FAQs
What materials do I need to build a concrete aquarium?
To build a concrete aquarium, you will need concrete mix, reinforcing steel bars, a mold, water, and a release agent.
How much does it cost to build a concrete aquarium?
The cost of building a concrete aquarium can vary depending on the size and design of the aquarium, but it typically ranges from $500 to $2,000.
Can I make a custom design for my concrete aquarium?
Yes, you can create a custom design for your concrete aquarium by building or purchasing a mold that matches your desired shape and size.
How long does it take to build a concrete aquarium?
The process of building a concrete aquarium can take anywhere from a few days to a few weeks, depending on the size and complexity of the design.
Is it difficult to maintain a concrete aquarium?
Not necessarily, but it may require more effort than maintaining a glass aquarium. Concrete aquariums need to be sealed and coated properly to prevent leaks and to withstand the harsh water conditions.
Can I add fish and plants to a concrete aquarium right away?
No, you need to wait for the concrete to cure completely before adding fish and plants to the aquarium. This typically takes at least 28 days.
Are there any safety precautions I should follow when building a concrete aquarium?
Yes, you should wear protective gloves and eyewear when handling concrete mix and reinforcing steel bars. It’s also important to follow proper ventilation procedures when working with concrete indoors.