Have you ever wondered how to create molds for your turtle aquarium? It may seem daunting at first, but with a little effort and creativity, you can have a custom habitat that both you and your shelled friend will enjoy. By making your own molds, you can create unique and interesting features that may not be readily available at the pet store. One way to start is by brainstorming different ideas for your aquarium.
Do you want your turtle to have a naturalistic environment, or something more whimsical? Once you have a general idea, you can begin researching different materials to create your molds. This can include items such as foam, silicone, and plaster. When creating your molds, it’s helpful to have a plan in place.
This could include sketches or even a 3D model. It’s also important to take into account the size of your turtle and how much space they will need. Once you have your molds created, the fun part begins – decorating! You can add rocks, plants, and other items to create a more realistic environment.
Your turtle will appreciate having different areas to explore and hide in. Overall, creating molds for your turtle aquarium is a fun and rewarding experience. Not only will you have a unique habitat for your pet, but you will also have the satisfaction of knowing that you created it yourself.
So why not give it a try? Your turtle will thank you for it.
Materials Needed
If you’re wondering how to make molds for your turtle aquarium, there are a few materials you’ll need to get started. Firstly, you’ll need some mold-making silicone, which can typically be found at any arts and crafts store. This will be the substance that you use to create your mold.
You may also need some clay or other modeling material to create the shape of your mold. Additionally, you’ll need a release agent, which will help the mold come off of your model more easily. Finally, you’ll need some tools to help you work with the silicone and shape your mold.
This may include things like sculpting tools, a small spatula, or a toothpick. With these materials in hand, you can begin working on your mold and create a perfect environment for your beloved pet turtles!
– Silicone
When it comes to working with silicone, there are several materials you’ll need to get started. The first and most obvious is silicone itself – whether you’re making molds, casting objects, or creating prosthetics, silicone is a versatile, durable material that can be used for a wide range of applications. You’ll also need a mold release agent to ensure that your silicone doesn’t stick to your molds, as well as a variety of tools for shaping, cutting, and smoothing your silicone as you work with it.
Depending on the type of project you’re working on, you may also need pigments, fillers, or other additives to achieve the desired properties and appearance in your final product. With the right materials and some practice, you can achieve excellent results with silicone and create everything from simple toys to intricate prosthetics that look and feel incredibly realistic.
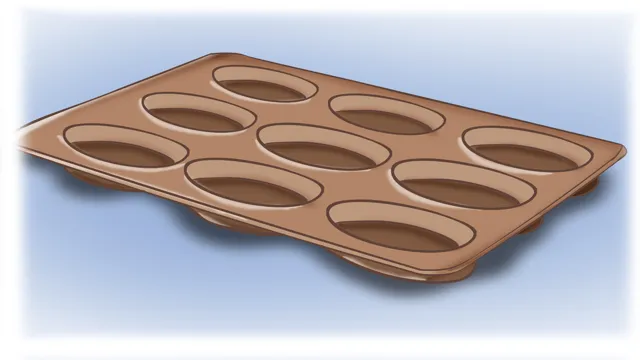
– Plasticine
Plasticine is a modeling clay that is versatile and easy to work with. To get started with plasticine, you will need a few basic materials. First and foremost, you will need plasticine clay in various colors.
Buying a few basic colors such as red, yellow, blue, black, and white are a good starting point. You will also need a work surface that can handle the clay. An art board or piece of wax paper works well.
Additionally, you may consider purchasing some modeling tools such as wire cutters, shaping tools, and texture tools. These will allow you to work with the clay more easily and create unique textures and shapes. Finally, a storage container to keep your clay from drying out between uses is essential.
With these basic materials, you’ll be able to create just about anything with your plasticine clay.
– Measuring cup
When preparing a recipe, having the right tools is essential to ensure the correct measurements and consistency. One of the most essential tools is a measuring cup, which helps you gauge the correct amounts of ingredients to be used. The measuring cup typically has markings and measurements indicated on its surface, making it easier for you to measure the various quantities of ingredients required for your recipe.
Depending on the recipe, a measuring cup can come in different sizes, such as half a cup, a quarter cup, one-third cup, or one cup. It is crucial to use the correct size of measuring cup as per the recipe requirements. A measuring cup is usually made of either plastic or glass, and it is essential to ensure that it is clean and free from any residue before measuring ingredients.
In conclusion, to produce delicious and consistent results, it is crucial to invest in a reliable, accurate, and appropriately sized measuring cup.
– Mixing bowl
When it comes to baking, having the right tools and ingredients is essential to creating delicious treats. One of the most important tools in a baker’s arsenal is the mixing bowl. To get the best results, it’s important to choose a mixing bowl that is durable, easy to clean, and large enough to accommodate the ingredients you are working with. (See Also: How to Make a Sweet Potato Holder in Aquarium Tank for Your Fish)
There are a variety of materials to choose from when it comes to mixing bowls, including glass, ceramic, stainless steel, and plastic. Glass is a great option for those who want to avoid any chemical leaching and allows for easy monitoring of the ingredients. Ceramic bowls are heavier and can retain heat, which is great for keeping butter at the perfect temperature while mixing.
Stainless steel is durable and easy to clean, making it a great option for frequent use, while plastic is lightweight and affordable, but not as durable as other materials. No matter which material you choose, it’s important to select a mixing bowl that is the right size for your needs. A bowl that is too small can result in a messy kitchen, while one that is too large can make it difficult to mix ingredients thoroughly.
With the right mixing bowl, you’ll be on your way to creating delicious baked goods in no time.
– Stirrer
If you are interested in making cocktails or mixing ingredients for food, you may need a stirrer. This tool is essential to stir drinks properly and incorporate all the ingredients together for a perfectly mixed beverage. A stirrer is a simple tool made of different materials, such as stainless steel, glass, or plastic.
The type of material you choose for your stirrer depends on your preference, the type of drink you are making, and the complexity of the ingredients involved. You can easily find a stirrer at any local kitchen supply store or online retailer. Just make sure to choose a stirrer that is easy to clean and comfortable to hold.
With a properly chosen stirrer, you can take your cocktail and cooking game to a whole new level.
– Utility knife
When it comes to getting the job done right, having the right tools is essential. And if you’re working on a DIY project or tackling a home improvement task, then you’ll definitely need a good utility knife. But what exactly do you need to get started? First things first, make sure you have a quality utility knife.
Look for one with a sturdy blade and a comfortable handle that feels good in your hand. Once you have your knife, you’ll also need some replacement blades, since they can dull quickly with use. Other materials you might want to have on hand include a ruler or measuring tape, a cutting mat or surface, and some scrap cardboard or foam board to protect your work surface.
With these materials at the ready, you’ll be able to tackle any cutting task with confidence. So go ahead and get started on that project – with the right tools at your fingertips, you’re sure to succeed!
Step-by-Step Guide
Making molds for your turtle aquarium can be a fun and easy DIY project. First, you will need to gather the necessary materials, including silicone mold putty, a mixing cup, and a stirring stick. Next, thoroughly clean and dry the item you want to make a mold of, such as a rock or piece of driftwood.
Then, mix the two parts of the silicone mold putty together using the stirring stick. Once the putty is mixed, quickly press it onto the item and shape it to cover all of its surfaces. Let the putty dry according to the manufacturer’s instructions, usually for about an hour or more.
Once it’s dry, carefully remove the putty mold from the item and use it to make your own identical replica. Whether you want to create a larger hideout for your turtle or multiple original decorations, making molds can be a cost-effective way to enhance your turtle’s habitat.
– Prepare the Work Area
Before you start any DIY project, it’s essential to prepare the work area for your safety and efficiency. Firstly, ensure that you have enough space to work and move around. Clean the area and remove any clutter or obstacles that may be hazardous.
Next, make sure that your tools and materials are organized and easily accessible. You don’t want to waste time searching for a tool or material in the middle of your project. Position your tools and materials close to your work area and have them organized in a way that makes sense to you.
Lastly, take the necessary safety precautions to protect yourself, such as wearing safety goggles, gloves, and a dust mask if needed. By properly preparing your work area, you’re bound to have a successful and safe DIY project.
– Create a Clay Model
If you’re an artist or sculptor, chances are you’ve dabbled in the art of creating clay models. Clay modeling is a great way to bring your ideas to life, whether you’re making a sculpture, a toy prototype, or a piece of jewelry. There’s something very satisfying about molding a lump of clay into the shape you desire, and watching your idea take shape right before your eyes.
Creating a clay model is a multi-step process that requires patience and skill, so it’s important to take your time and not rush the process. The first step is to choose your clay – you’ll want to select a type that is easy to work with and can hold its shape well. Once you’ve chosen your clay, you’ll need to gather your tools and equipment and start molding, starting with the rough shape and then adding details.
To start, begin by mapping out the basic shape and proportions of your model. If you’re working on something like a human figure, it’s important to get the proportions right early on, so you don’t have to do as much correcting later on. Once you have the basic shape of your model roughed out, you can start thinking about the details you want to add, like facial features or clothing patterns. (See Also: How to Create a Faux Stream in Fish Aquarium: A Step-by-Step Guide)
Keep in mind that you’ll need to be patient and work slowly to achieve the level of detail you want – it’s easy to accidentally squish or distort your model if you apply too much pressure or try to hurry the process. One helpful tip is to work in small sections – focus on one area at a time, like the face or hands, and get that area as detailed and precise as possible before moving on to the next section. This will help maintain the integrity of your model and minimize mistakes.
Another helpful technique is to use an armature – a wire frame or skeleton – to give your clay structure and prevent it from collapsing or sagging as you work. Overall, creating a clay model requires patience, practice, and attention to detail. It’s a rewarding process that allows you to turn your vision into a three-dimensional reality.
With the right tools, techniques, and mindset, you can bring your ideas to life and create a stunning clay model that you’ll be proud of.
– Make a Silicone Mold
Making a silicone mold is easier than you might think, and it’s a great way to replicate shapes and forms that you love. Here’s a step-by-step guide on how to make your own silicone mold. First, you’ll need a clean and smooth model of the shape you want to replicate.
You can use a variety of materials, such as clay, plastic, or wood. Then, prepare your silicone according to the manufacturer’s instructions and pour it over your model, making sure it covers the entire surface. Allow the silicone to cure for the recommended time, usually around 24 hours.
Once it’s cured, carefully remove the silicone mold from the model. If you want to make multiple copies, use a release agent before pouring the resin or plaster into the mold. Finally, allow the casting material to set and then remove it from the mold.
Voila! You now have a faithful copy of your original shape. Making a silicone mold is a fun and rewarding process that anyone can do. So why not give it a try and see what you can create?
– Remove the Model from the Mold
Once your resin has set in the mold, it’s time to remove the model. This can be a delicate process, as you don’t want to damage your finished piece or the mold itself. Begin by gently twisting and wiggling the model, trying to loosen it from the mold.
You can also use a soft tool to gently pry the edges of the model away from the mold. If your mold has a seam, make sure to work on one side at a time, gently working the model out of the mold. Be patient and take your time, as rushing can lead to mistakes and damage to your project.
With a bit of care and patience, you can successfully remove your model from the mold and move on to the finishing steps of your project.
– Pour the Resin into the Mold
Now that you’ve prepared everything for your resin project, it’s time to pour the resin into the mold! This is a crucial step, as it will determine the final outcome of your project. Start by slowly pouring the resin into the mold, making sure not to overflow it. Using a measuring cup can help you control the amount of resin you pour.
As you pour, you may notice bubbles forming in the resin. Don’t worry; this is normal! Simply use a heat gun or a torch to pop the bubbles. Work your way around the mold, making sure to cover every corner evenly.
If you’re working on a larger project, you may want to pour the resin in layers to prevent overheating and ensure a more even distribution. Once you’ve poured all the resin you need, leave it to cure for the recommended time. And voila! You’ve successfully poured resin into a mold.
With some creativity and patience, you can create beautiful and unique resin projects that are sure to impress.
Finishing Touches
If you’re looking to make your own molds for your turtle aquarium, there are a few finishing touches you’ll want to consider. First and foremost, it’s important to make sure that your mold is completely dry and free of excess plaster before you start using it. This will prevent any residue or debris from getting into your turtle’s habitat.
Additionally, you may want to consider adding some extra details to your mold to make it even more realistic and appealing to your pet. This could include adding some rocks or other natural elements to the mold, or even painting it with some aquarium-safe colors to give it a more vibrant and attractive look. Ultimately, the key to making a great mold for your turtle aquarium is to take your time, be patient, and put in the effort to make it as high-quality as possible.
With a little bit of creativity and elbow grease, you can create a mold that your turtle will love and enjoy for years to come. (See Also: How to Get Aquarium Driftwood to Sink: Tips and Tricks for Submerged Wood Decor)
– Remove any imperfections
As you come to the end of a project, it’s important to not let complacency set in. This is where the finishing touches come in! To really elevate your work, take the time to remove any imperfections. This could be anything from editing out a typo to smoothing out a rough edge on a physical creation.
These small details may seem insignificant, but they make all the difference in creating a polished final product. Think of it like putting a cherry on top of a sundae – it doesn’t change the flavor, but it makes it look so much more enticing. By taking the extra effort to ensure that every aspect of your work is top-notch, you’ll show your audience that you truly care about their experience.
So, take a step back and give your work a critical eye. Chances are, there’s something you can improve upon. And as you make those final adjustments, remember that every little bit counts towards creating a successful end result.
– Buff and Polish the surface
When it comes to giving your project that final touch, buffing and polishing the surface can make all the difference. Whether it’s a piece of woodwork, metalwork, or any other material, buffing and polishing can enhance its appearance and give it a smooth, professional look. Buffing is the process of using a buffing wheel and a polishing compound to remove any small imperfections on the surface.
Once the buffing is done, polishing comes in. Polishing involves using a finer abrasive compound to smooth out the surface and give it a shine. The result is a surface that looks new and polished, giving it that wow factor that catches the eye.
So, if you’re looking to give your project that extra shine that it deserves, buffing and polishing is the way to go.
Conclusion
In conclusion, creating molds for your turtle aquarium may seem daunting at first, but with the right materials and a little bit of creativity, you can mold a habitat that your shelled friend will adore. Just remember, slow and steady wins the race and don’t be afraid to shell-ebrate your success with a turtle who is sure to give you a hard-earned shell high-five.”
FAQs
What materials do I need to make molds for my turtle aquarium?
To make molds for your turtle aquarium, you will need silicone molding rubber, a mold release agent, a mixing container, and mixing tools.
How do I apply mold release agent to my mold?
To apply mold release agent to your mold, you can use a spray or a brush. Make sure to cover all surfaces of the mold and let it dry before pouring your molding rubber.
How much molding rubber do I need for my mold?
The amount of molding rubber you need will depend on the size and shape of the mold you are making. Follow the manufacturer’s instructions for mixing and measuring the right amount of rubber.
How long does it take for the molding rubber to dry?
The drying time of the molding rubber will depend on the type of rubber you are using and the temperature and humidity of your environment. Generally, it takes 24-48 hours to fully cure.
How do I remove the mold from my aquarium after the molding rubber has dried?
Once the molding rubber has dried, you can carefully remove the mold from your aquarium by peeling it off or cutting it open with a sharp knife.
How do I make multiple molds of the same shape?
To make multiple molds of the same shape, you can use your original mold as a pattern and make a silicone mold box around it. Then, pour the molding rubber into the box to create more molds.
Can I use other types of molding materials besides silicone rubber?
Yes, there are other types of molding materials you can use such as plaster of Paris, polyurethane, or latex rubber. However, silicone rubber is known for its durability and flexibility, making it a popular choice for aquarium molds.